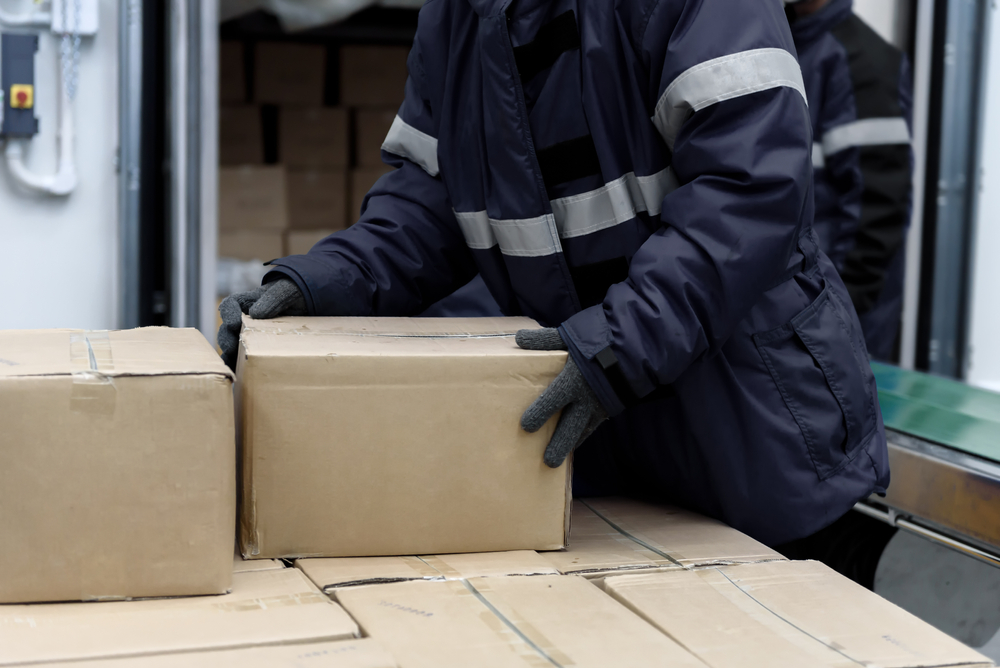
If you work in food or pharmaceutical industry, you must know how difficult it is to manage and transport these perishable items. Failure to regulate temperature along the delivery will cause damaged products, customer dissatisfaction and wastage of manufacturing effort.
Cold chain logistics is the solution to such problems. It’s an advanced technology that regulates the temperature for a safe supply of temperature sensitive products.
But what does it exactly involve?
Flexi Couriers is here to guide.
In this blog post, we’ll help you know everything about cold chain logistics. We’ll discuss its components, benefits and work principles as well. Additionally, at Flexi Couriers, we provide temperature efficient logistic service for safe deliveries of your valuable products.
Let’s start with the basics of cold chain transport.
What is Cold Chain Logistics?
Cold chain logistics (also called chill chain logistics) refers to the advanced storage methods and temperature-controlled shipping of perishable goods. These temperature sensitive goods include food items, beverages, and biopharmaceutical products.
This service helps the manufacturing in keeping their products in good condition and provides safe transport to customers.
A specific low-temperature range has to be maintained for each type of product i.e., some products have to be refrigerated, some must be frozen, while others require deep freezing. Failure to maintain the right temperature leads to product spoilage and, ultimately, financial losses.
This complicated task involves various temperature-controlled packaging methods, equipment, and technologies, to assure the safety of products.
Components of Cold Chain Logistics
Key components of the process include:
1. Packaging of Goods
Insulation materials and designs protect the products from temperature changes during transport. It includes the use of materials such as quilts, reefers, dry ice, gel packs, liquid nitrogen, and eutectic plates.
2. Monitoring the Delivery
Systems and tools are used to track the temperature of products along the journey. These technologies provide alerts if the temperature deviates from the required range so that prompt solutions can be applied.
3. Transport System
Refrigerated transport is the most vital part of the cold chain process.
Specialised vehicles and containers with installed temperature control systems are used for the journey. Products are loaded and unloaded quickly to reduce outside exposure.
4. Safe Handling
The process of loading, unloading, and moving goods is done in such a way that the required temperature range isn’t disturbed. Facilities are used for safe and fast processing with sanitation protocols.
5. Temperature-Controlled Storage
Warehouses incorporate technologies that maintain a controlled temperature. It includes refrigeration units and other systems to keep products safe till dispatching.
These elements work together to help maintain following temperature conditions.
Cold Chain Temperature Requirements
Temperature-controlled shipping has to maintain the different ranges of temperature according to the type of products.
The temperatures generally suggested are:
Product Type | Temperature Range |
Fresh Produce (meals, food items) | Ambient temperature range |
Fruits, Vegetables, Dairy Products | Slightly lower temperatures |
Pharmaceutical Drugs & Vaccines | Ultra-low temperature storage below -70°C |
Frozen Meat and Seafood | Deep-freezing |
Standards and Regulations for Temperature Sensitive Products
As the cold chain is responsible for the delivery of food items and health essentials such as drugs or vaccines. Adherence to food and health industry standards is a must while handling these items. Following regulatory guidelines are followed generally.
- Transport of all pharmaceuticals and other items related to the health industry is regulated by WHO guidelines. Cold chain management must be fully aware of them and follow them.
- For food and grocery items, the Australian Food and Grocery Council imposes a series of guidelines for the safe transport of perishable goods. Their regulations protect and manage the refrigerated and frozen food industry.
Benefits of Cold Chain Logistics
Cold chain logistics is preferred over normal supply chain, for temperature-controlled shipping, due to its following distinct services:
- Product Safety
Cold Chain keeps the products safe and intact during transport. Maintaining the integrity of products is essential for the efficacy of companies and minimizing product loss. Hence, lowering the possibility of customer complaints or legal actions.
- Quality Preservation
Refrigerated Transport maintains the quality of temperature-sensitive products. So, troubles like product loss, costly fines, health risks, and reputational damage to companies can be reduced.
- Regulatory Compliance
Food and pharmaceutical companies have to follow the rules of regulatory food and health authorities. Cold chain logistics help businesses meet these regulatory standards.
- Reduced Waste
By maintaining temperature, the risk of spoilage and wastage of valuable items is reduced. Saving the effort of waste handling will help in better management of resources and finances.
Learn more: How Refrigerated Transportation Has Changed the World?
Differences Between Cold Chain and Normal Supply Chain
Demands of cold chain logistics differs from a normal supply chain in several key ways:
Aspect | Cold Chain Logistics | Normal Supply Chain Logistics |
Temperature Control | Strict temperature control. | No temperature control |
Equipment | Refrigerated containers and cold storage warehouses. | Standard containers |
Monitoring | Continuous temperature monitoring. | Basic or no temperature monitoring. |
Regulations | Subjected to strict regulations (e.g., GDP, GMP). | Limited regulations related to temperature. |
Packaging | Refrigerated trucks, and Insulated packaging materials | Standard packaging materials. |
Shelf life | Shorter shelf life because goods can easily parish | Longer shelf life |
Data Tracking | Real-time data tracking and documentation. | Basic data tracking. |
Cost | Costly due to specialized infrastructure, equipment, and procedures | Low cost due to less complexity. |
Training | Specific training of staff on temperature control. | Staff require standard training. |
Product Types | Perishable products such as Food items, Pharmaceuticals, etc. | Used for non-temperature-sensitive products. |
6 Common Challenges Faced During Cold Chain Packing & Logistics
These issues are faced commonly while dealing with the transport of temperature sensitive products.
1. Electronic Malfunctions
Electronic devices like refrigerators and coolants can get damaged or malfunction during use. Continuous monitoring should be done to prevent these issues.
2. Infrastructure Maintenance
The temperature sensitive transport vehicle and warehouse with advanced equipment are difficult to maintain and consume a huge share of finance, resources, and time.
3. Damage to Equipment
If a refrigerator or cooler is unable to close properly, the temperature inside it can’t be regulated. These temperature fluctuations can severely impact the quality of goods. Additionally, condensation build-ups can lead to slippery surfaces and product contamination.
4. Negligence to Guidelines & Rules
Neglecting storage or transport guidelines by any staff member can cause the quality to be compromised. It can result in complaints, financial losses, and a damaged reputation of the company.
5. Packaging and Handling Issues
Inadequate packaging can disrupt temperature regulation. Also, delays in loading and unloading can cause excessive heat exposure. Temperature-reliant goods can degrade and significant loss can be caused to the company.
6. Transportation Delays
Unexpected delays from the distributors or disruptions during transport (like weather conditions or emergencies) are common phenomena. Since the cold chain is time sensitive so, any increase in delivery time will damage the quality of perishable products.
Now, let’s see how cold chain management deal with these challenges.
Cold Chain Logistics Management | 7 Effective Strategies
Temperature sensitive products must be preserved and transported under organized conditions. These best practices are required to maintain the integrity and quality of products throughout the cold chain packing & logistics.
1. Regular Maintenance
Every type of equipment needs regular checking, issue diagnosis, and upkeep to sustain its proper form. Management should arrange maintenance schedules for refrigeration units, vehicles, and monitoring systems.
2. Product Preparation & Packaging
Products should undergo a prior checking procedure to make sure that they are at the right temperature for packaging and transport. Appropriate packaging materials and proper measures help in effective temperature control.
3. Staff Training
Given the complexity of the cold chain and its logistics, staff should be properly trained before beginning to work. They should learn the guidelines of regulatory bodies, the importance of temperature control, and proper handling techniques.
4. Detailed Documentation
In case of any emergency or mishap, a complete and thorough record of your handling can help in managing the legal and administrative concerns. Keep a detailed record of temperature readings, time measures, storage conditions, and any important incident.
5. Emergency Management
Strategic planning and execution are essential to manage all the challenges and unforeseen situations. Have a ready-to-execute plan B to deal with temperature deviations, transport delays, and equipment failures.
6. Monitoring and Data Analysis
Continuous supervision and transparent analysis can keep track of the trends and possible issues. The administration should collect the data from temperature sensors and tracking devices, detect any problems, and arrange prompt measures to get a smooth process.
7. Simulation Modeling
Simulation modeling is used to understand which conditions can cause failure or damage to a product and what loads it can withstand. It played an important role in the distribution of COVID-19 vaccines making it a successful logistics operation.
Are you looking for a reliable and temperature-controlled transport?
Reach Out Flexi Couriers for Efficient Cold Chain Logistics Services Across Western Australia
Flexi Couriers offers specialized cold chain logistics and provide you with easy and efficient temperature-regulated transport. We carry out the expert handling of valuable goods with our trained professionals and advanced equipment.
We are handling operations in Perth and surrounding regions for a variety of businesses and industries. Our tri-temperature technology helps maintain three separate temperatures for frozen, chilled, and ambient goods.
Along with transport, we also provide a storage facility with our temperature sensitive warehouse to help in managing and growing your business.
Contact us to get an expert logistics partner.
Visit our website for further information.
FAQs
Q1: What is cold storage in logistics?
It is a specific storage facility provided by Cold chain logistics to keep the products in the required temperature range until dispatching. It consists of a temperature-monitored warehouse with advanced cooling equipment.
Q3: What are the three main components of a cold chain?
Three main components of cold chain are temperature monitored storage, packaging, and transport.
Q4: What is the difference between cold chain and supply chain?
Cold chain and normal supply chain differs in terms of temperature control, equipment, monitoring systems, product type and complexity of tasks.
Q5: What is the temperature in cold chain logistics?
Different temperature ranges are maintained in cold chain depending on type of product. E.g. ambient for fresh produce, -70°C for vaccines and drugs, and deep freezing for meat and seafood.